Join us in advancing geotechnical engineering. Email: una@kellegco.com
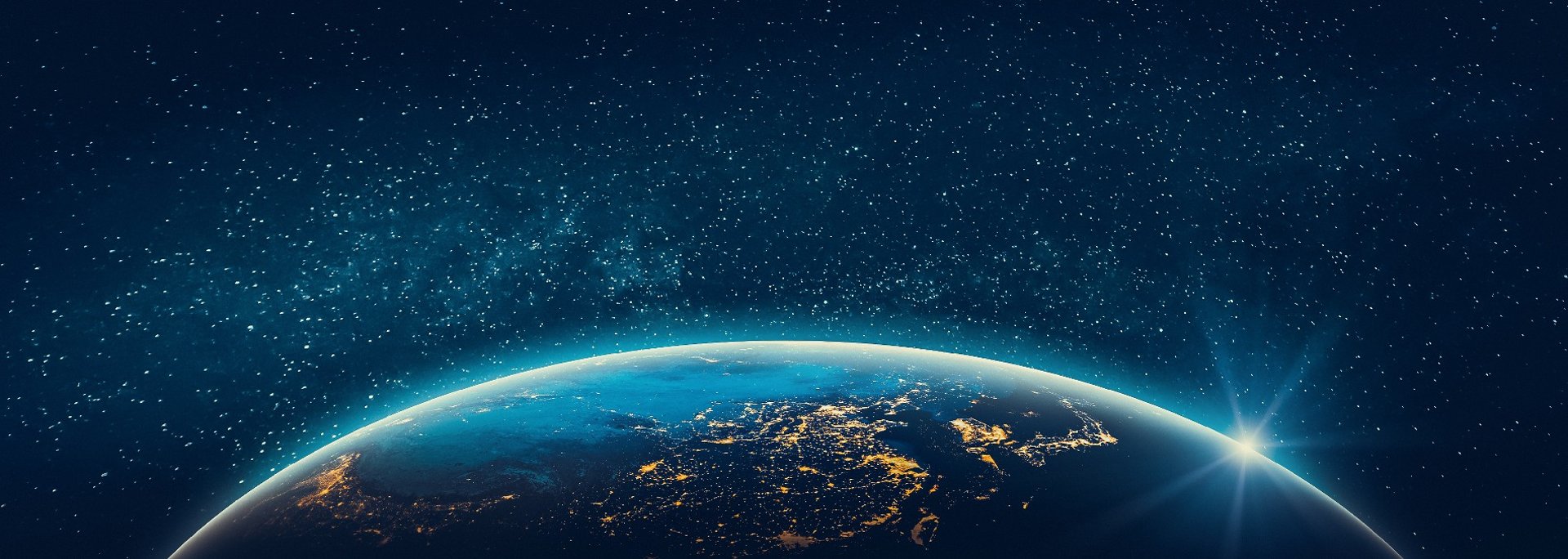
What is Hot-Dip Galvanization
Hot-dip galvanization process involves coating the metal with zinc by immersing it in a bath of molten zinc at around 450 °C (842 °F).
Una
10/25/2024
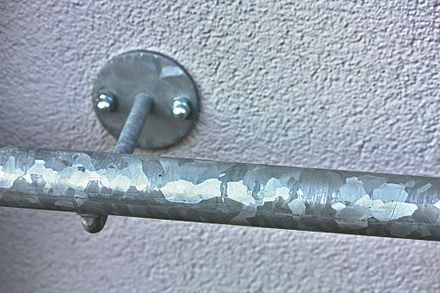
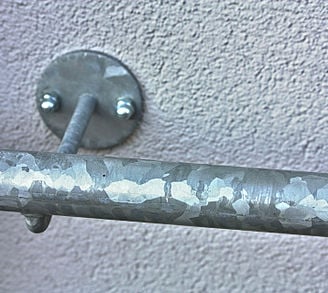
Hot-dip galvanization is a widely-used method for protecting iron and steel from corrosion. This process involves coating the metal with zinc by immersing it in a bath of molten zinc at around 450 °C (842 °F). The resulting galvanized metal is known for its durability and corrosion resistance, making it a preferred choice for various applications, from construction to automotive manufacturing. This article delves into the intricacies of hot-dip galvanization, exploring its process, benefits, applications, and more.
The Process of Hot-Dip Galvanization
The hot-dip galvanization process involves several crucial steps to ensure a robust and durable zinc coating on the steel surface. Here's a detailed look at each step:
1. Cleaning: The steel is first cleaned using a caustic solution to remove any oil, grease, dirt, and paint. This step is essential to ensure that the zinc can adhere properly to the steel surface.
2. Rinsing: The caustic cleaning solution is thoroughly rinsed off the steel to prevent any residue from interfering with the subsequent steps.
3. Pickling: The steel is then pickled in an acidic solution, usually hydrochloric or sulfuric acid, to remove mill scale and any remaining rust. This step is critical for creating a clean, reactive surface for zinc bonding.
4. Rinsing Again: After pickling, the steel is rinsed again to remove any traces of the acidic solution.
5. Fluxing: A flux, typically zinc ammonium chloride, is applied to the steel to prevent oxidation of the cleaned surface when exposed to air. The flux also aids in the wetting and adhesion of the liquid zinc to the steel.
6. Drying: The flux-coated steel is allowed to dry to enhance the bonding process during galvanization.
7. Galvanizing: The dried steel is then dipped into a molten zinc bath, where it is held until the temperature of the steel equilibrates with the bath. This step forms a metallurgical bond between the zinc and the steel.
8. Cooling: The galvanized steel is cooled in a quench tank to reduce its temperature and prevent any undesirable reactions with the atmosphere.
The Metallurgical Bond
The hot-dip galvanization process creates a strong metallurgical bond between the zinc and the steel. This bond consists of several distinct iron-zinc alloy layers, providing exceptional durability and corrosion resistance. When exposed to the atmosphere, the zinc reacts with oxygen to form zinc oxide (ZnO), which further reacts with carbon dioxide (CO2) to form zinc carbonate (ZnCO3). This zinc carbonate layer is a stable and protective barrier that shields the steel from further corrosion.
Applications of Hot-Dip Galvanized Steel
Hot-dip galvanized steel is used in various applications due to its excellent corrosion resistance and cost-effectiveness. Some common applications include:
- Construction: Galvanized steel is extensively used in construction for roofing, walling, safety barriers, and handrails. Its durability and corrosion resistance make it ideal for outdoor structures exposed to harsh weather conditions.
- Automotive Manufacturing: Electrogalvanized sheet steel is often used in automotive manufacturing to enhance the corrosion performance of exterior body panels. While this process achieves lower coating thicknesses than hot-dip galvanization, it provides a strong bond and effective protection.
- Consumer Appliances: Many household appliances, such as washing machines and refrigerators, use galvanized steel to prevent rust and extend their lifespan.
- Metal Pails: Galvanized steel is commonly used to manufacture metal pails, providing a durable and corrosion-resistant container for various applications.
- Heating and Cooling Ducts: Most heating and cooling duct systems in buildings use galvanized steel to prevent corrosion and ensure long-lasting performance.
Advantages of Hot-Dip Galvanization
Hot-dip galvanization offers several advantages over other corrosion protection methods:
- Cost-Effective: Compared to stainless steel, hot-dip galvanized steel provides excellent corrosion resistance at a lower cost. This makes it an attractive option for many industries.
- Long Life Cycle: The metallurgical bond between zinc and steel ensures a long-lasting protective coating, reducing maintenance and replacement costs.
- Self-Healing Properties: Zinc's electropositive nature means it can protect exposed steel through galvanic corrosion, continuing to offer protection even when the coating is damaged.
- Versatility: Hot-dip galvanized steel can be used in various environments, from urban and industrial settings to rural and marine conditions, due to its robust corrosion resistance.
Welding and Galvanized Steel
While galvanized steel can be welded, precautions must be taken to manage the toxic zinc fumes released during welding. These fumes can pose health risks if inhaled, so proper ventilation and protective equipment are essential. Additionally, welding temperatures should be controlled to prevent peeling of the zinc coating at high temperatures. According to the American Galvanizers Association, the recommended maximum temperature for long-term, continuous exposure of hot-dip galvanized steel is 200 °C (392 °F).
Lead in Hot-Dip Galvanization
Lead is often added to the molten zinc bath during hot-dip galvanization to improve fluidity and drainage properties, prevent floating dross, and protect the kettle from uneven heat distribution. However, environmental regulations in the United States discourage the use of lead in the galvanization process due to its adverse environmental and health effects. Alternatives such as primary Z1 grade zinc or used secondary zinc are preferred to minimize lead content.
Hot-Dip Galvanized Steel Strip
Steel strips can be hot-dip galvanized in a continuous line, resulting in a product commonly referred to as galvanized iron. This material combines the strength of steel with the corrosion resistance of zinc, making it suitable for applications like roofing, walling, safety barriers, handrails, consumer appliances, and automotive body parts. The continuous galvanization process ensures uniform coating and consistent quality.
Batch Galvanizing vs. Electrogalvanizing
Individual metal articles, such as steel girders or wrought iron gates, can be hot-dip galvanized through a process called batch galvanizing. In this method, the metal is dipped into the molten zinc bath in batches, ensuring thorough coating of each piece. However, modern techniques like electrogalvanizing have largely replaced hot-dip galvanization for these applications. Electrogalvanizing deposits a layer of zinc from an aqueous electrolyte by electroplating, forming a thinner and stronger bond compared to hot-dip galvanization.
Environmental Considerations
The hot-dip galvanization process, while effective in protecting steel from corrosion, has environmental implications. The use of lead in the zinc bath poses risks to the environment and human health. Therefore, stringent regulations are in place to limit lead content and encourage the use of alternative methods. Additionally, the process generates waste products like spent pickling acid and zinc ash, which require proper disposal to prevent environmental contamination.
Future Trends in Hot-Dip Galvanization
The hot-dip galvanization industry is continuously evolving to meet the demands of modern applications and environmental standards. Some emerging trends include:
- Environmentally Friendly Processes: Efforts are underway to develop galvanization processes that minimize environmental impact. This includes reducing lead content and improving waste management practices.
- Advanced Coating Technologies: Innovations in coating technologies aim to enhance the durability and performance of galvanized steel. This includes the development of new fluxes and alloys that improve adhesion and corrosion resistance.
- Automated Galvanization Lines: Automation and advanced monitoring systems are being integrated into galvanization lines to improve efficiency, quality control, and safety.
Conclusion
Hot-dip galvanization is a vital process for protecting steel from corrosion, extending its lifespan, and enhancing its performance in various applications. From construction and automotive manufacturing to consumer appliances and HVAC systems, galvanized steel plays a crucial role in modern infrastructure and technology. Understanding the process, benefits, and applications of hot-dip galvanization helps industries make informed decisions about material selection and corrosion protection strategies.
As environmental concerns and technological advancements continue to shape the industry, the future of hot-dip galvanization looks promising, with ongoing efforts to improve sustainability, efficiency, and performance. Whether for large-scale construction projects or everyday household items, hot-dip galvanized steel remains a reliable and cost-effective solution for corrosion resistance.