Join us in advancing geotechnical engineering. Email: una@kellegco.com
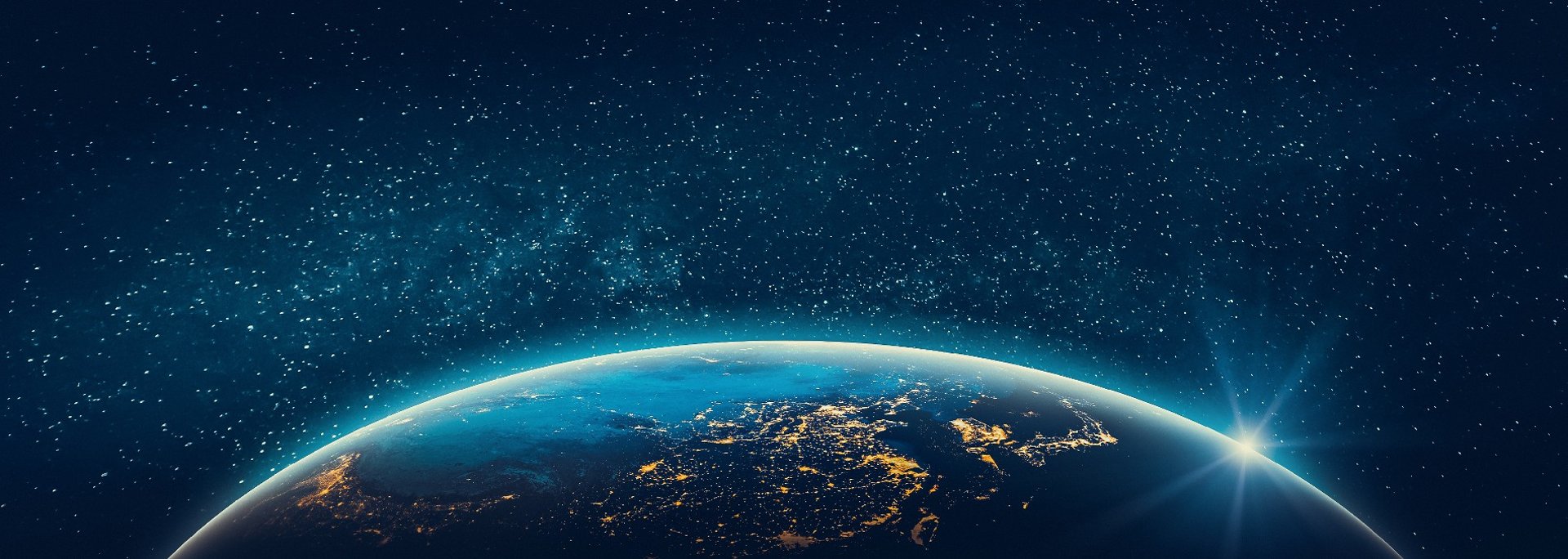
What are Chemical Resin Anchors?
Chemical resin anchors are a type of fixing system that uses a combination of a resin adhesive and a hardener to secure anchors into concrete, brick, stone, or other masonry substrates.
Una
10/28/2024
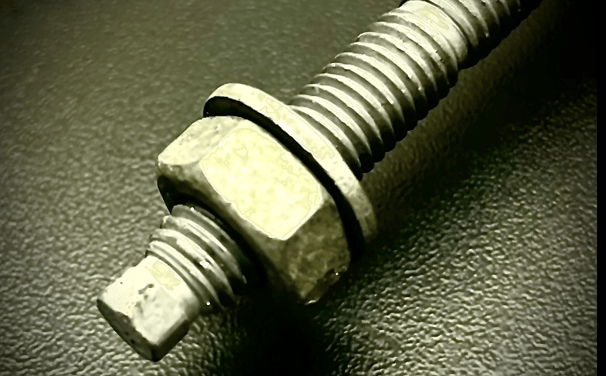
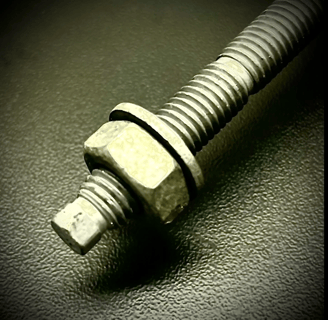
Chemical resin anchors are widely recognized as one of the strongest and most reliable options for securing studs or anchors into concrete. Whether you're working on a construction project, a renovation, or a DIY task, the need for a stable and secure fixing cannot be overstated. Unlike traditional mechanical anchors, chemical resin anchors use a two-part system where a resin and a hardener are mixed and injected into the drilled hole before inserting the stud or anchor. This method creates an exceptionally strong bond that evenly distributes the load across the entire embedded length of the anchor.
In this comprehensive guide, we will explore the key advantages of chemical resin anchors, how they work, and step-by-step instructions for installation. We’ll also delve into their various applications and why they are an ideal choice for many different scenarios, especially when the substrate is irregular or fixings are close to an edge.
What Are Chemical Resin Anchors?
Chemical resin anchors are a type of fixing system that uses a combination of a resin adhesive and a hardener to secure anchors into concrete, brick, stone, or other masonry substrates. The system is designed to be used in drilled holes where the resin is injected before inserting the anchor. The resin then hardens, creating a secure bond that holds the anchor in place.
Unlike mechanical anchors, which rely on expansion to hold the anchor in place, chemical resin anchors provide a bond that distributes the load across the entire embedded depth of the anchor. This feature is particularly beneficial in situations where mechanical anchors might cause the substrate to crack or fail, especially when placed near the edge of a structure.
Key Advantages of Chemical Resin Anchors
Chemical resin anchors offer numerous advantages that make them an ideal choice for various applications. Here are some of the most significant benefits:
1. High-Temperature Resistance
Chemical resin anchors can withstand extremely high temperatures, with some types capable of resisting temperatures up to 350°C. This makes them suitable for use in environments where heat resistance is critical, such as in industrial settings, near furnaces, or in areas prone to fire exposure.
2. Excellent Chemical Resistance
These anchors offer outstanding resistance to a wide range of chemicals, including oils, acids, bases, solvents, and alcohols. This property makes them ideal for use in environments where exposure to harsh chemicals is a concern, such as chemical plants, laboratories, or industrial facilities.
3. Corrosion and Oxidation Resistance
Chemical resin anchors are highly resistant to ageing, oxidation, and corrosion, ensuring long-term durability even in challenging environments. This resistance makes them suitable for use in outdoor applications, marine environments, or areas exposed to moisture and salt.
4. No Expansion Stress on Substrate
Unlike mechanical anchors, chemical resin anchors do not create expansion pressure on the substrate. This feature is especially beneficial when working with fragile or brittle materials or when fixing points are close to edges. The absence of expansion stress minimizes the risk of substrate failure.
5. Uniform Load Distribution
The load applied to a chemical resin anchor is spread evenly across the full embedment of the anchor, as opposed to being concentrated at specific points, as is the case with mechanical anchors. This uniform distribution of load enhances the anchor's holding power and reduces the likelihood of substrate failure.
6. Seismic and Vibration Resistance
Chemical resin anchors are exceptionally effective in seismic conditions and areas with high levels of vibration. Their ability to absorb and distribute dynamic forces makes them ideal for use in structures located in earthquake-prone regions or in machinery installations where vibration is a concern.
7. Versatile Applications
Chemical resin anchors can be used with hollow sockets to create removable fixing points, making them versatile for a wide range of applications. They are suitable for both temporary and permanent fixings in various construction, renovation, and DIY projects.
8. Safe for Drinking Water and Pools
With WRAS (Water Regulations Advisory Scheme) approval, certain types of chemical resin anchors are safe for use in environments where they may come into contact with drinking water or be submerged in swimming pools. This certification ensures that the materials used do not contaminate water sources.
9. Fire Resistance
Many chemical resin anchors are F240 fire-rated, meaning they can withstand exposure to fire for up to 240 minutes. This fire resistance makes them a reliable choice for applications where fire safety is a concern, such as in building construction or industrial installations.
10. ETA Approval
European Technical Assessment (ETA) approval is a certification that guarantees the performance of construction products in Europe. Chemical resin anchors with ETA approval meet stringent quality and safety standards, ensuring their reliability in critical applications.
Applications of Chemical Resin Anchors
Given their strength, versatility, and durability, chemical resin anchors are used in a wide range of applications. Some common uses include:
1. Structural Fixings
Chemical resin anchors are widely used in structural applications, such as securing steel beams, columns, or brackets to concrete structures. Their ability to withstand high loads and resist seismic forces makes them ideal for structural fixings in buildings, bridges, and other infrastructure.
2. Masonry and Stonework
These anchors are often used in masonry and stonework to secure heavy fixtures, such as balustrades, railings, or façade elements. Their non-expanding nature ensures that the masonry or stone substrate is not damaged during installation.
3. Industrial Installations
In industrial settings, chemical resin anchors are used to secure machinery, equipment, and piping systems. Their resistance to chemicals, high temperatures, and vibrations makes them suitable for harsh industrial environments.
4. Retrofit and Repair
Chemical resin anchors are ideal for retrofit and repair projects, where existing structures need to be reinforced or new fixings are required. They are often used to install additional reinforcements in older buildings or to replace damaged mechanical anchors.
5. Seismic Applications
In regions prone to earthquakes, chemical resin anchors are used to secure critical components, such as HVAC systems, electrical panels, and heavy equipment. Their seismic resistance helps prevent damage during seismic events.
6. Marine and Coastal Environments
The corrosion resistance of chemical resin anchors makes them suitable for use in marine and coastal environments, where exposure to saltwater and moisture is a concern. They are commonly used to secure dock fixtures, seawalls, and other marine structures.
How to Install Chemical Resin Anchors
Installing chemical resin anchors is a straightforward process that involves just a few steps. Here’s a detailed guide on how to properly install these anchors:
Step 1: Drill the Hole
Begin by drilling the hole to the required diameter and depth. The diameter of the hole should be slightly larger than the diameter of the stud or anchor. For example, an 8mm stud would require a 12mm hole. SDS (Special Direct System) drill bits are commonly used for this purpose, as they provide clean and precise holes.
Step 2: Clean the Hole
Thoroughly clean the drilled hole to remove all debris, dust, and loose particles. This step is critical to ensuring a strong bond between the resin and the substrate. Use a combination of air pumps, hole brushes, and vacuum cleaners to achieve a clean hole. The recommended cleaning method involves two rounds of air pumping, followed by two rounds of hole brushing, and then a repeat of both steps.
Step 3: Inject the Chemical Resin
Using an applicator gun, inject the chemical resin into the hole. It’s important to use an extension tube that reaches the bottom of the hole to avoid trapping air. Start injecting the resin from the bottom and slowly withdraw the tube while continuing to inject, ensuring the hole is filled evenly. Mark the extension tube with tape at two-thirds of the hole depth to help control the amount of resin used and prevent waste.
Different types of resins require different applicator guns. Pure epoxy resins, for instance, mix in the nozzle and are typically used with wider-bodied guns. Polyester resins set faster than epoxy resins and are better suited for situations where rapid curing is needed.
Step 4: Insert the Stud or Anchor
Wrap the threaded portion of the stud with electrical tape to protect it from resin contamination. Then, carefully insert the stud or anchor into the resin-filled hole, rotating it slightly as you insert it to ensure full coverage of the resin around the stud. The electrical tape should be removed after the stud is fully inserted.
Step 5: Allow the Resin to Cure
Once the stud or anchor is in place, allow the resin to cure for the recommended time before applying any load. Curing times vary depending on the type of resin, ambient temperature, and humidity. It’s essential to follow the manufacturer’s guidelines for curing times to ensure a strong bond.
In colder environments, the curing time may be longer, so plan accordingly. Once the resin has fully cured, the fixing is ready for use.
Common Types of Chemical Resin Anchors
Chemical resin anchors come in various formulations, each designed to meet specific performance requirements. Understanding the differences between these types is essential for selecting the right product for your project. Here are the most common types of chemical resin anchors:
1. Epoxy Resin Anchors
Epoxy resin anchors are renowned for their superior bonding strength and long-term durability. They provide excellent adhesion to a wide range of substrates, including concrete, stone, and masonry. Epoxy resins are particularly well-suited for heavy-duty applications that require high load-bearing capacity, such as structural connections, seismic retrofits, and industrial installations. Although they have a longer curing time compared to other resins, the resulting bond is incredibly robust and resistant to environmental stresses such as moisture, chemicals, and temperature fluctuations.
2. Polyester Resin Anchors
Polyester resin anchors are a popular choice for general-purpose applications where quick installation is needed. These resins cure rapidly, making them ideal for projects with tight timelines. Polyester resin anchors are commonly used for medium-duty fixings in masonry, brick, and blockwork. While they offer good bonding strength, they are not as resistant to high loads or harsh environmental conditions as epoxy resins. However, their ease of use and fast setting times make them a go-to option for many DIY projects and non-critical applications.
3. Vinylester Resin Anchors
Vinylester resin anchors provide a balance between the quick curing time of polyester resins and the high performance of epoxy resins. They are known for their excellent resistance to chemicals, moisture, and extreme temperatures. This makes them a versatile option for both indoor and outdoor applications, including marine environments, industrial settings, and areas with aggressive chemical exposure. Vinylester resins cure faster than epoxy resins but still offer strong bonding properties, making them suitable for medium to heavy-duty fixings where environmental resistance is key.
Summary
Chemical resin anchors are an advanced and reliable solution for securing studs and anchors into concrete and other masonry substrates. Unlike traditional mechanical anchors, chemical resin anchors utilize a resin and hardener to create a bond that evenly distributes load across the entire embedment. This method offers numerous advantages, including high-temperature and chemical resistance, corrosion resistance, no expansion stress on the substrate, and exceptional performance in seismic and high-vibration conditions. Additionally, chemical resin anchors are safe for use in drinking water and fire-rated environments.
The article details the step-by-step process for installing chemical resin anchors, emphasizing the importance of proper hole cleaning, resin injection, and curing. It also highlights the different types of chemical resin anchors—epoxy, polyester, and vinylester—each suited for specific applications, from heavy-duty structural fixings to quick-setting DIY projects.
With their versatile applications and strong, durable performance, chemical resin anchors are an ideal choice for a wide range of construction, industrial, and renovation projects.