Join us in advancing geotechnical engineering. Email: una@kellegco.com
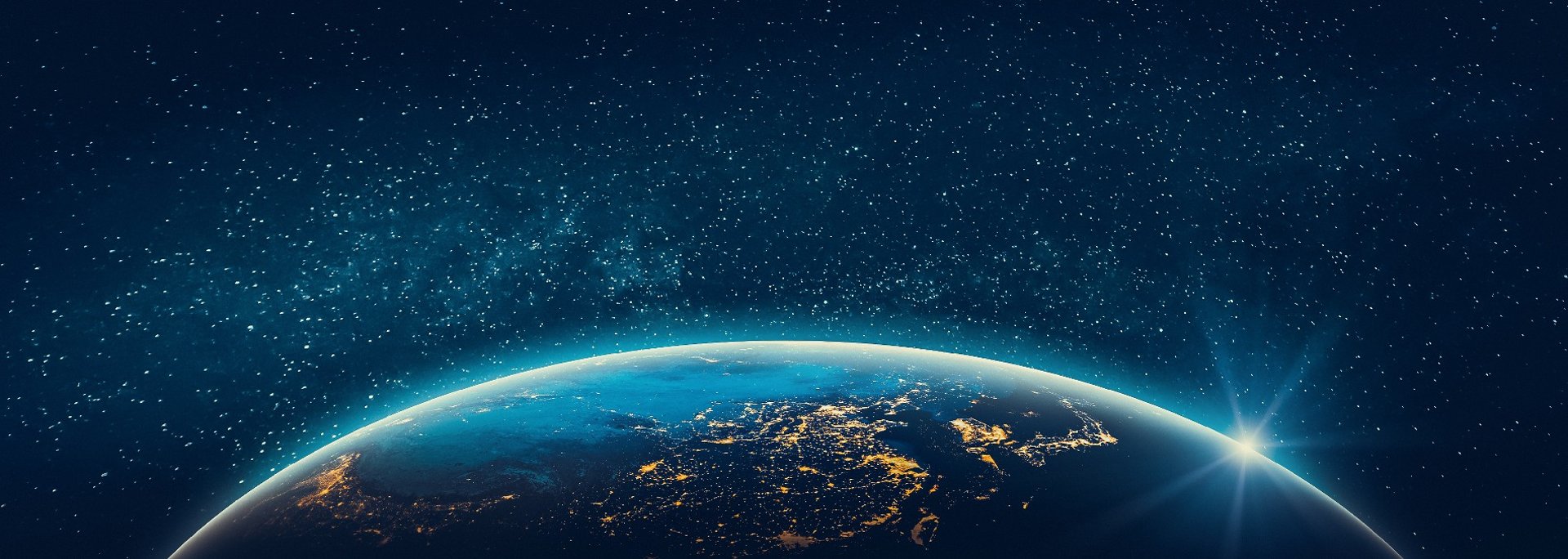
Understanding Pipe Roofing in Tunnel Construction
The technique of pipe roofing is frequently employed in conventional tunnel drives following New Austrian Tunneling Method (NATM) principles to enhance overall safety and manage poor ground conditions effectively.
Hannah
7/8/2024
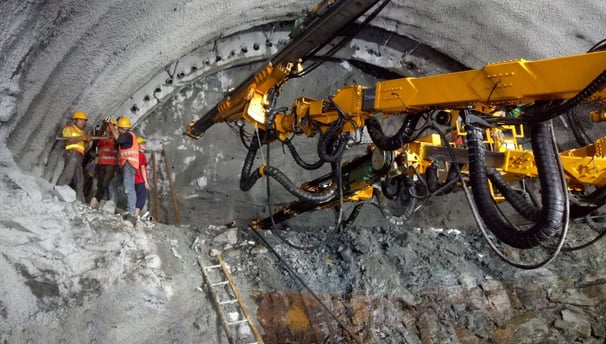
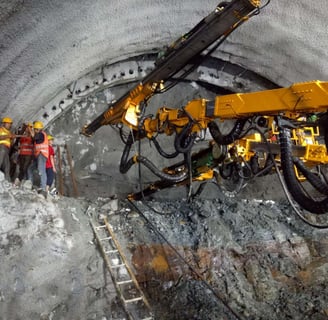
Introduction
In the realm of tunnel construction, especially in urban areas with challenging ground conditions and minimal surface cover, the technique of pipe roofing has gained significant prominence. This method is frequently employed in conventional tunnel drives following New Austrian Tunneling Method (NATM) principles to enhance overall safety and manage poor ground conditions effectively. Pipe roofing is instrumental in addressing hazard situations, such as tunnel collapses and limiting surface settlements. This article delves into the intricacies of pipe roofing, offering a comprehensive overview of its definition, main features, installation process, and practical applications. Drawing from practical experiences across various projects, we will also explore the current limits of its application.
Definition of a Pipe Roofing System
The term "pipe roofing system" lacks a universally accepted definition due to the absence of standardized design protocols. Various terminologies have been used by different authors to describe this tunnel support system. For instance, Hoek (2003) referred to it as the "pipe forepole umbrella," Kim et al. (2004) called it the "umbrella arch method," Miura (2003) termed it the "pipe forepiling method," Gibbs (2002) named it the "steel pipe canopy," and Volkmann et al. (2006) described it as "pipe roof supports."
Despite the varied nomenclature, all these definitions converge on the concept of a tunnel support system comprising a specialized drilling and casing mechanism, typically combined with grouting works and the interaction between steel pipes and the surrounding ground. Additionally, the system often includes the application of face anchors to ensure the stability of the tunnel face.
Main Features of Pipe Roofing Systems
Equipment and Installation
Pipe roofing systems can be installed using specialized equipment or common drilling jumbos. Each approach has its own set of advantages and limitations. While specialized equipment offers precision and efficiency, common drilling jumbos provide greater flexibility, albeit with some constraints in drilling techniques, such as the type and size of hammer, drilling/casing systems, and flushing media.
Material Specifications
In Central Europe, typical pipe roofing involves steel pipes with outer diameters of 76 mm, 89 mm, 114 mm (most common), or 139 mm, and wall thicknesses ranging from 5 to 10 mm. These pipes are either thread-coupled or welded together. The pipes are installed in the crown of the tunnel with a drilling inclination of about 4-6°. Parts of coupled drill bits, known as ring bits, usually remain in the ground. In very soft ground, less expensive bits can be left in place.
Installation Process
The installation process involves simultaneous drilling and pipe insertion using a hydraulic drill hammer with specific parameters for percussion and rotation. A common practice in Central Europe is to use 15-meter pipes with a 114 mm diameter, overlapping by 5 meters, resulting in a saw-tooth profile in the longitudinal direction with varying geometries of steel ribs or lattice girders. At the starting point, a slight widening of the profile is necessary.
Design Considerations
The economic design of a pipe roof should not rely solely on the designer's assumptions but must consider the actual face conditions. A typical layout of pipe roof geometry includes 25-40 pipes per pipe roof, installed during top heading activities in common railway tunnels.
Applications and Benefits
Enhancing Tunnel Safety
One of the primary applications of pipe roofing is to improve the overall safety of tunnel construction, particularly in weak ground conditions. By providing additional support to the tunnel crown and face, pipe roofing mitigates the risk of collapses and stabilizes the surrounding ground.
Managing Surface Settlements
In urban areas, controlling surface settlements is crucial to prevent damage to adjacent buildings and infrastructure. Pipe roofing effectively limits surface settlements by reinforcing the tunnel structure and distributing loads more evenly.
Overcoming Challenging Ground Conditions
Pipe roofing is particularly beneficial in overcoming poor ground conditions, such as loose soil, high groundwater levels, and fractured rock masses. The combination of drilling, casing, and grouting works strengthens the ground and enhances its load-bearing capacity.
Case Studies and Practical Experiences
Practical experiences from various projects highlight the effectiveness of pipe roofing in different scenarios. For instance, in a railway tunnel project in Central Europe, pipe roofing was employed to navigate through a section with highly fractured rock and high groundwater inflow. The system provided the necessary support to ensure the stability of the tunnel and prevent water ingress.
In another project involving a metro tunnel in an urban area, pipe roofing was used to limit surface settlements and protect nearby buildings. The method proved successful in maintaining the structural integrity of the tunnel and minimizing the impact on the surrounding environment.
Current Limits of Application
While pipe roofing has proven to be a valuable technique in tunnel construction, it is essential to recognize its current limitations. One of the primary challenges is the lack of standardized design protocols, which can lead to variations in implementation and performance. Additionally, the method may not be suitable for all ground conditions, particularly in extremely hard rock or highly cohesive soils.
Conclusion
Pipe roofing has emerged as a critical technique in tunnel construction, offering numerous benefits in terms of safety, surface settlement management, and adaptability to challenging ground conditions. By leveraging the knowledge of site geologists and parameters gained from drilling and grouting works, engineers can create safe and efficient tunnel driving conditions. As the method continues to evolve, further research and standardization efforts are necessary to enhance its applicability and effectiveness in a broader range of scenarios.