Join us in advancing geotechnical engineering. Email: una@kellegco.com
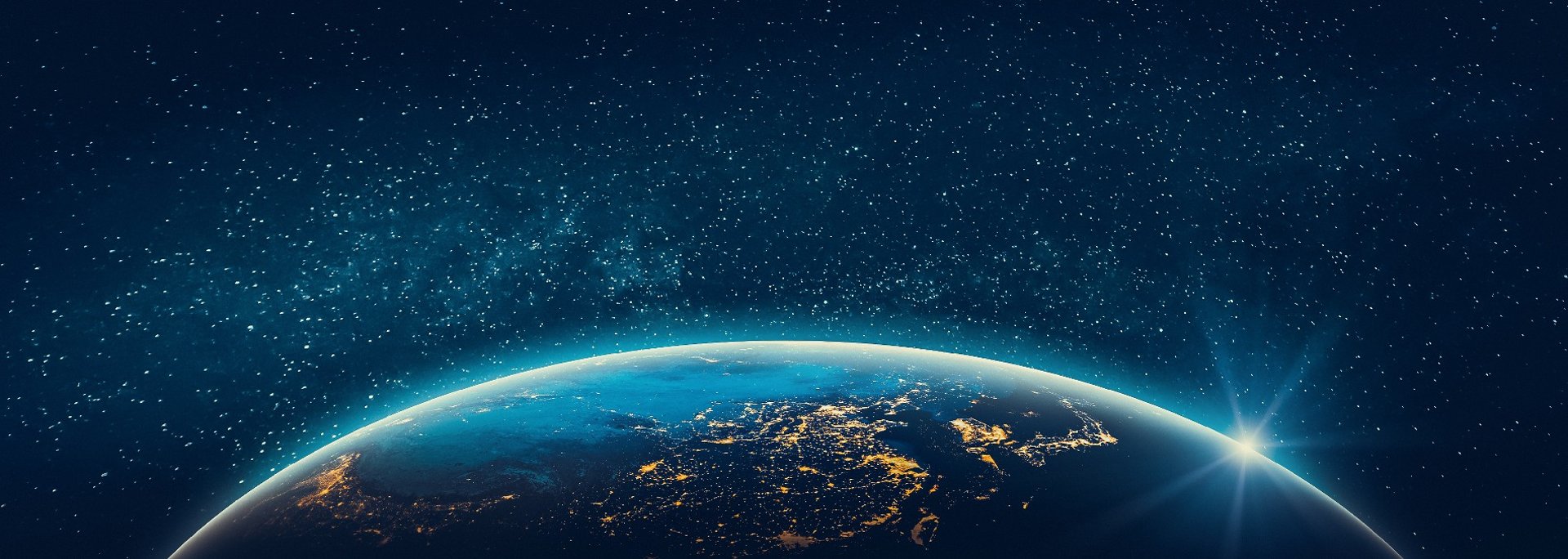
What Type of Drill Bit Is Used to Drill Holes into the Rock?
Different drill bits are suitable for rocks of varying hardness and properties due to their unique structure and design. From top hammer rock drill bits to DTH drill bits to rotary drill bits and PDC drill bits, each type of drill bit has its specific application scenarios and advantages.
Una
7/3/2024

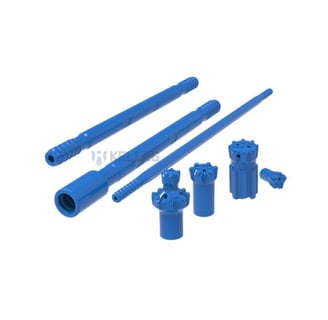
Choosing the proper type of drill bit for drilling operations in rock is critical. Rocks have different properties such as hardness, density, brittleness, or toughness, which requires us to choose the right drill bit type according to specific engineering needs and environmental conditions. The appropriate drill bit can not only improve drilling efficiency and reduce operating costs but also ensure the quality of the hole wall, thereby meeting the drilling accuracy requirements of various engineering projects. Next, we will explore which types of drill bits are suitable for drilling holes in rock and analyze their respective characteristics and advantages.
Top hammer rock drill bit
The top hammer rock drill bit is indispensable in various mining projects. It consists of a high-quality steel drill bit body and unique carbide buttons. The carbide buttons are made through a sophisticated welding process. According to the characteristics of different rock formations, top hammer rock drill bits are available in various types, such as chisel bit, cross bit, X bit, and button bit.
Chisel bit: this type is suitable for light rock drills, performs well when drilling rock formations with low hardness, and is easy to sharpen.
Cross bit and X bit: they are suitable for rock drills with higher impact power and have excellent resistance to radial abrasion when drilling fractured and highly abrasive rock formations.
l Button bit: with the help of large impact power rock drills, button bits can show higher rock drilling speeds and longer service life, and the holes drilled are more rounded.
Down-the-hole drill bit
The down-the-hole drill bit is another professional drilling tool. It uses the spline of the drill bit body to connect with the hammer to break the rock deep into the hole. According to the different wind pressures, down-the-hole drill bits are available in three types: high wind pressure, medium wind pressure, and low wind pressure. It features various end face designs, including convex, flat, concave, and deep concave center types.
Convex type: it is more efficient when drilling medium-hard and hard rocks, but the straightness of the hole is slightly inferior.
Flat type: it is robust and durable, suitable for a wide range of rock types, especially hard and ultra-hard rocks.
Concave type: the unique concave design helps the drill bit maintain centering performance and provides excellent straightness and a fast powder removal effect.
Deep concave center type: it is specifically designed for drilling deep holes to ensure hole straightness and is suitable for soft to medium-hard rocks.
Rotary drill bits
The rotary drill bits have a place in the drilling industry with their unique working method. Its cutting teeth alternately contact the bottom of the well, with low rock-breaking torque and a small contact area but high specific pressure, so it can easily cut into the formation. Rotary drill bits are suitable for various formations, from soft to hard. In particular, roller cone bits have become the preferred tool in petroleum and geological exploration.
PDC drill bit
PDC drill bits, or polycrystalline diamond composite drill bits, have a round shape and are welded onto a cylindrical cutting tool. They are widely used in geological exploration, coalfield drilling, and oil exploration. There are various types of PDC drill bits, each optimized for specific rock conditions.
PDC drill bits for geological exploration: suitable for soft to medium-hard rock formations, and the new composite piece can even cope with rock formations with a hardness of ten.
PDC drill bits for coalfield drilling: designed for the relatively soft rock formation characteristics of coalfields, widely used in anchor drill bits and three-wing drill bits, etc.
PDC drill bits for oil exploration: specifically designed for oil and gas field drilling, it is the most technically demanding and expensive PDC drill bits.
How to choose the right drill bit
There are several factors to consider when selecting a drill bit for use in drilling holes in rock:
Rock type and properties
Different rocks have different physical properties, such as hardness, toughness, toughness, and tightness. These properties will directly affect the choice of drill bits and the drilling effect. When choosing a drill bit, we need to select the right drill bit type according to the specific type and properties of the rock.
Drilling requirements
When selecting a drill bit, it's pivotal to consider drilling requirements such as hole diameter, depth, and hole wall quality. Choose the appropriate drill bit type and specifications based on these specific needs. For instance, opt for a larger diameter drill bit when creating a larger hole diameter. When ensuring high-quality hole walls, choose a drill bit with superior cutting performance and stability.
Cost and budget
Different types of drill bits have different production costs and sales prices. When choosing a drill bit, you need to consider the limitations of cost and budget. Under the premise of ensuring the quality of drilling, try to opt for a drill bit product with a higher-cost performance.
Conclusion
Choosing the appropriate type of drill bit is crucial when drilling holes in the rock. Different drill bits are suitable for rocks of varying hardness and properties due to their unique structure and design. From top hammer rock drill bits to DTH drill bits to rotary drill bits and PDC drill bits, each type of drill bit has its specific application scenarios and advantages.
Top hammer rock drill bits perform well in moderately hard rock formations due to their high-quality steel and alloy teeth. DTH drill bits maintain efficient drilling rates and excellent hole wall quality when breaking rocks with their specially designed end faces. Rotary drill bits, with their cutting teeth design that alternately contacts the bottom of the well, can operate with ease in various formations. The PDC drill bit, with its high-hardness polycrystalline diamond composite, has demonstrated excellent performance in hard rock drilling.
In summary, the type of drill bit to choose depends on the specific rock type, project requirements, and cost budget. By carefully evaluating these factors, we can ensure that the most suitable drill bit is selected when drilling holes in the rock, thereby improving work efficiency, reducing costs, and meeting the project's requirements for drilling accuracy.