Join us in advancing geotechnical engineering. Email: una@kellegco.com
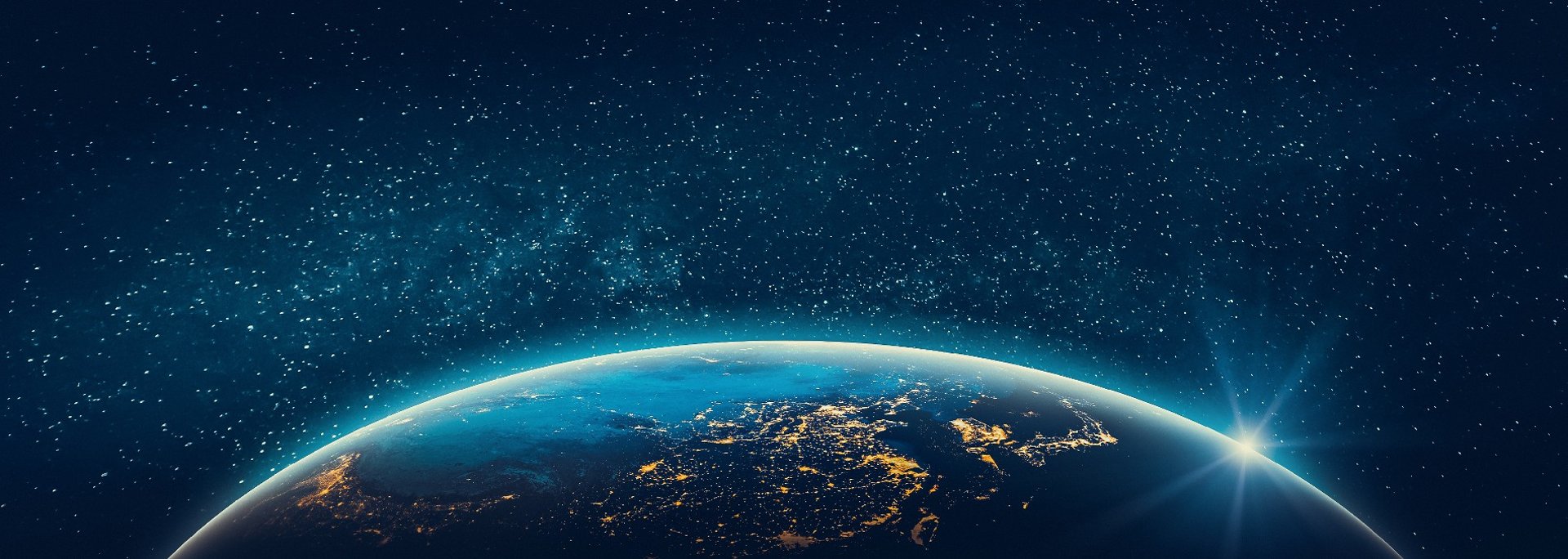
The Evolution of Drifter Drills in Mining and Civil Engineering
A drifter drill is a specialized tool used to penetrate rock, typically for drilling holes to place explosives in rock blasting or for use in quarrying operations like plug and feather quarrying.
Una
11/22/2024
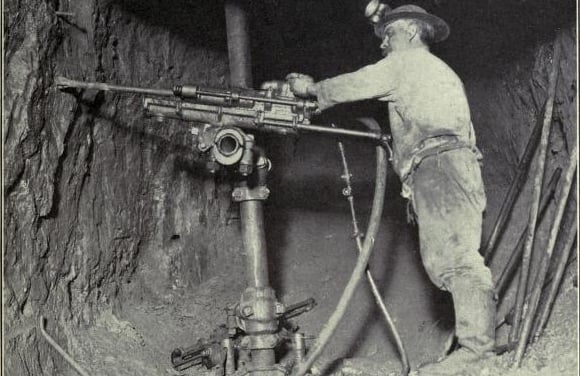
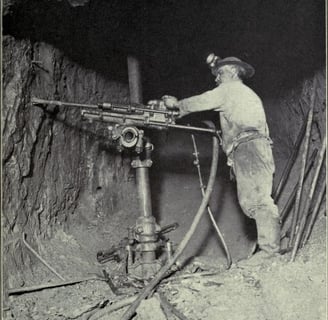
In the world of mining and civil engineering, drifter drills, commonly known as rock drills, are indispensable tools used to drill into rock formations. These machines are designed to create holes for a variety of purposes, including placing explosives for rock blasting or preparing holes for quarrying processes. Over time, the functionality, design, and power sources of these tools have evolved significantly, making them safer, more efficient, and more versatile.
What is a Drifter Drill?
A drifter drill is a specialized tool used to penetrate rock, typically for drilling holes to place explosives in rock blasting or for use in quarrying operations like plug and feather quarrying. These machines are integral to the mining and civil engineering sectors, where large-scale rock excavation is required. Although simple forms of rock drills may appear rudimentary, modern versions are often powerful machines that employ various mechanical systems to achieve their function.
Mechanisms of Operation
Drifter drills can be powered through several mechanisms, including hand operation, steam, compressed air (pneumatics), hydraulics, or electricity. The power source generally dictates the size, capability, and specific use of the machine.
1. Manual Drilling: In its simplest form, a drifter drill may consist of a long chisel or steel that requires physical force, like a sledgehammer, to drive it into the rock.
2. Powered Drills: Modern drifter drills are powered by steam, compressed air, hydraulics, or electricity. The transition from manual to powered drills has revolutionized the speed and efficiency of rock drilling in mining and construction.
Drifter drills are categorized into two basic types:
- Percussion Drills: These use a reciprocating motion to drive a sharp bit into the rock.
- Rotary Drills: These use a rotating motion to grind and cut into rock formations.
Both types of drills have distinct uses depending on the material being drilled and the required hole specifications.
Historical Background of Drifter Drills
The history of rock drills dates back several centuries, with early methods relying on basic mechanical tools. The simplest form of a rock drill was essentially a chisel that was struck by a sledgehammer to create holes in rock.
Early Drilling Methods
Mark Twain, famous for his adventures in the American West, once described his experience working as a silver miner in the 1860s, using the manual drilling process:
"One of us held the iron drill in its place and another would strike with an eight-pound sledge—it was like driving nails on a large scale. In the course of an hour or two, the drill would reach a depth of two or three feet, making a hole a couple of inches in diameter."
This process, though labor-intensive, was effective for creating holes for explosives. A team of 2-4 men would work a single hole, with each taking turns pounding the chisel. In one day, a skilled team could achieve up to 50 feet (15 meters) of drilling.
Steam and Powered Drills
By the late 19th century, manual methods were increasingly replaced by powered drills, particularly steam-powered drills. The first steam drill was invented by Richard Trevithick in 1813, but it was in the following decades that steam drills gained popularity in surface quarries rather than underground mines, owing to the proximity to boilers. These steam-powered drills were capable of drilling faster and more efficiently than manual techniques, although they had their limitations, such as requiring an external power source and being heavy and difficult to maneuver.
The advent of electric and pneumatic drills in the early 20th century marked a significant turning point in drilling technology. The widespread use of compressed air, in particular, allowed for lighter, more portable drills that could be used in underground mining, significantly improving worker safety and productivity.
Rock Drills in Popular Culture
The evolution of drilling technology also became the stuff of American folklore, with the legendary story of John Henry. According to the myth, John Henry—a steel driver—competed against a steam-powered drill in a race to dig through a mountain. Although Henry won the contest, the physical exertion led to his collapse and death. This story symbolized the tension between manual labor and industrial mechanization during the rise of the machine age.
Configurations of Modern Drifter Drills
Today, modern drifter drills come in various configurations, each suited for specific types of drilling tasks. The primary distinction lies in how the drill is mounted, the type of motion used (percussive or rotary), and the mechanisms that power the device.
Percussion Drills
Percussion drills operate on the principle of repeated impact, with a hammer-like mechanism delivering a series of blows to the drill bit. This repetitive motion breaks the rock into smaller fragments, which are then cleared out of the borehole. Percussion drills are typically used for drilling into hard, compact rock formations.
Features of Percussion Drills:
- Reciprocating motion: A piston or hammer strikes the drill bit repeatedly.
- High-impact energy: Ideal for breaking hard rock formations.
- Shorter lifespan: Percussion drills tend to wear out faster due to the intense impact force.
Rotary Drills
Rotary drills use a rotating motion to cut into rock. These drills often employ a rotating drill bit with sharp edges or abrasives to grind through rock formations. Rotary drills are commonly used for softer rock types or when a smoother, more uniform hole is required.
Features of Rotary Drills:
- Continuous rotation: The drill bit spins continuously, grinding through the rock.
- Less impact: Rotary drills generate less shock and are better suited for softer rock formations.
- Efficient for large-scale drilling: Rotary drills can bore large holes quickly and efficiently.
Mounting Configurations
Drifter drills can be mounted in different ways depending on the nature of the drilling task. These configurations are designed to ensure the stability and accuracy of the drill.
- Tripod Mounting: For vertical drilling, especially in quarrying applications, drifter drills are often mounted on tripods with attached weights. These provide the necessary downward force to penetrate rock surfaces.
- Jack Mounts or Columns: For horizontal drilling, the drill is mounted on columns that lock into the ceiling and floor to maintain stability and pressure against the rock.
- Quarry Bar: A rock drill mounted on a long rod, or quarry bar, allows the drill to be moved along a predetermined line. This is used to create a straight row of holes, typically for the plug and feather technique, which splits rock along the desired line.
Drill Bits for Rock Drills
The type of drill bit used in rock drilling plays a crucial role in the effectiveness of the operation. Rock is inherently abrasive and hard, so ordinary steel drill bits would wear out quickly. For this reason, drill bits are typically fitted with harder materials that can withstand the rigors of drilling.
Tungsten Carbide Inserts
Most rock drills are fitted with tungsten carbide inserts, a highly durable material that resists wear and tear. Tungsten carbide is ideal for drilling into hard rock formations, as it is significantly harder than steel and can maintain its sharpness for longer periods.
Diamond-Coated Bits
For specialized applications, such as drilling through harder materials like granite or marble, rotary rock drills often use diamond-coated bits. Diamond, the hardest known material, is set into the drill bit in a process that ensures the diamond protrudes from the surface. As the bit wears down, the diamond continues to shield the bit from wear until it gradually wears away. This feature is particularly useful for drilling through very hard rocks or even frozen soil.
Heated Drill Bits
In specific conditions, such as drilling through frozen soil or ice, heated drill bits are used to melt through the material. These bits use an electrical or thermal source to generate heat, which is then transferred to the drill bit.
Safety Concerns and Dust Mitigation
One of the primary concerns when using drifter drills is the generation of dust. The fine dust produced during drilling operations can be hazardous to workers' health, causing respiratory issues such as silicosis, a lung disease common among miners. In response to these concerns, modern rock drills are equipped with water-cooling systems that flood the borehole with water. This helps to capture the dust particles, improving air quality and reducing the risk of inhalation.
Benefits of Water Cooling Systems:
- Dust suppression: Water captures and prevents dust from being inhaled by workers.
- Lubrication: The water cools and lubricates the drill bit, preventing overheating and improving its lifespan.
- Increased safety: By reducing airborne dust, water cooling systems help create a safer working environment for drill operators.
Conclusion
Drifter drills have come a long way from their early manual origins to the powerful, machine-driven devices used in today's mining and civil engineering projects. The evolution of rock drilling technology, including the development of percussion and rotary drills, various mounting configurations, and specialized drill bits, has made these machines more efficient and versatile than ever before. While safety concerns such as dust generation remain, modern innovations like water cooling systems have helped mitigate these risks, ensuring that drifter drills continue to play an essential role in rock excavation and construction projects worldwide.
As the mining and civil engineering industries continue to evolve, the drifter drill will remain an indispensable tool in drilling technology, ensuring that operations run smoothly, efficiently, and safely across the globe.