Join us in advancing geotechnical engineering. Email: una@kellegco.com
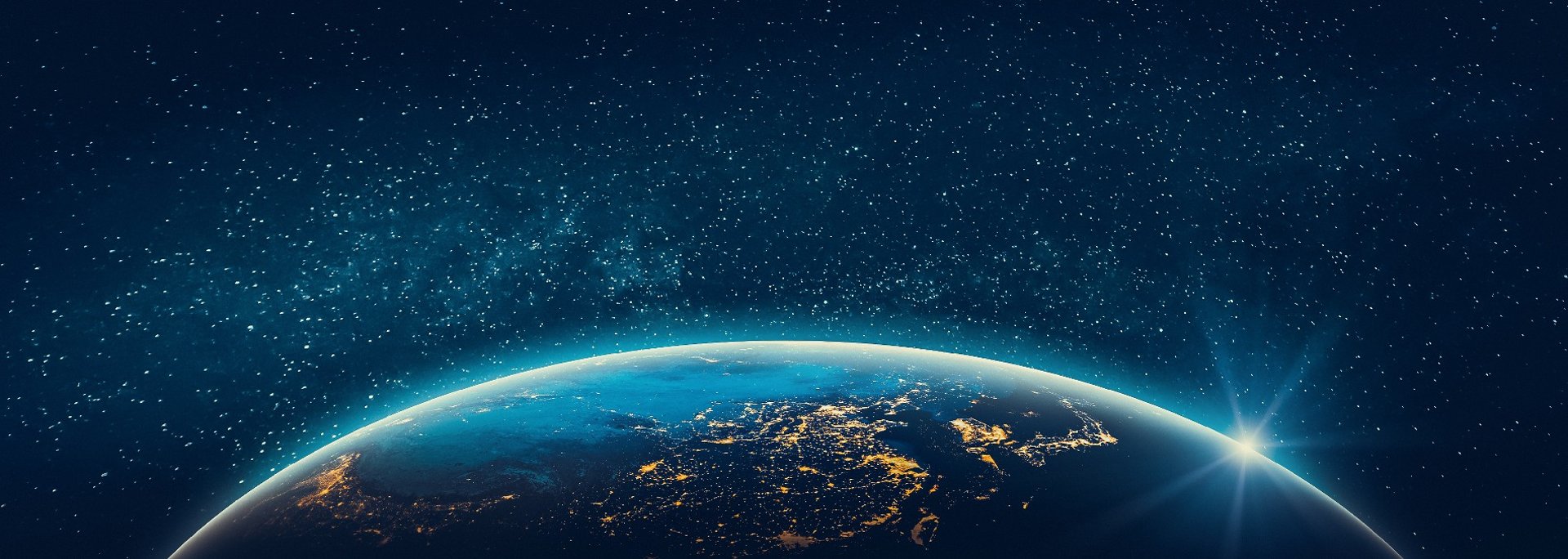
What Are the Benefits of Having Carbide Tips on Drill Bits?
The application of cemented carbide in rock drill bits enhance rock drilling efficiency and construction safety while reducing construction costs and improving the environment.
Una
6/26/2024
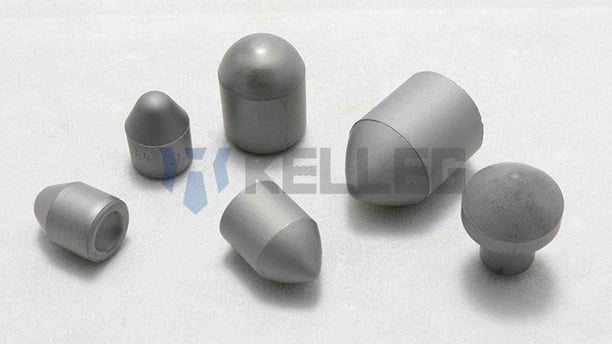
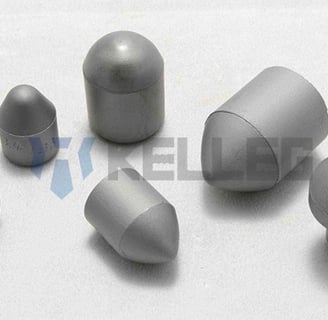
In mining, tunneling, and building foundation construction, rock drill bits are critical rock-breaking tools, and their performance directly affects work efficiency and cost. With the continuous advancement of materials science, the use of cemented carbide in rock drill bits is becoming more and more widespread, and its many benefits have made this material the industry's first choice. So, what are the benefits of cemented carbide used in rock drill bits?
High hardness and wear resistance
Cemented carbide is a composite material made of rigid compounds of refractory metals (WC, TiC, TaC, NbC, etc.) and bonding metals (Co, Ni, Fe, etc.) through powder metallurgy. Among them, tungsten carbide gives cemented carbide extremely high hardness and wear resistance. During the rock drilling process, the rock drill bits are constantly rubbed against and impact hard rocks. The high hardness and wear resistance of cemented carbide can ensure that the drill bit reduces wear and thus prolongs its service life.
Excellent impact resistance
Rock drill bits must withstand both the friction from the rocks and the immense impact forces during operation. The bonding metal (such as Co) in cemented carbide can effectively combine the rigid phase particles to form a uniform and dense microstructure, thereby improving the impact resistance of the alloy. It makes the cemented carbide drill bit less likely to break or chip when impacted, ensuring the stability and safety of the work.
Good thermal conductivity and thermal stability
During high-speed rock drilling, the friction between the rock drill bit and the rock generates lots of heat. If this heat cannot be emitted in time, it will cause the drill bit to overheat, affecting its performance and service life. Carbide, with its good thermal conductivity and thermal stability, can quickly transfer heat away from the drill bit, preventing excessive internal temperatures and ensuring the continuous operation of the drill bit.
High processing accuracy and stability
Cemented carbide materials can be made into various sizes of drill bits through precise processing to meet different engineering needs. At the same time, the microstructure of cemented carbide is uniform and dense, which can maintain high dimensional accuracy and shape stability, ensuring that the drill bit will not deform or change in size during long-term use.
Reduce costs and improve economic efficiency
Although the initial cost of cemented carbide is relatively high, its overall cost is relatively low considering its excellent performance and service life. Using carbide drill bits can significantly reduce replacement frequency and maintenance costs, improve work efficiency, and bring greater economic benefits to the enterprise.
Strong adaptability and wide application range
Carbide drill bits are suitable for rock drilling operations of various hardnesses and can be customized according to engineering needs to meet the requirements of different working conditions. No matter in harsh environments such as high temperature, high pressure, or high humidity, carbide drill bits can maintain good performance and ensure the smooth progress of the project.
Improve engineering quality and increase competitiveness
Using carbide drill bits can improve the accuracy and efficiency of rock drilling, reduce rock crushing and pulverization, and thus improve the quality of the project. At the same time, high work efficiency and stable performance can also enhance the competitiveness of enterprises and win more market share.
Selection suggestions and precautions for carbide rock drill bits
When choosing carbide rock drill bits, it's essential to consider specific construction conditions, rock properties, rock drill models, and other relevant factors comprehensively. Generally speaking, for rocks with higher hardness, it's advisable to choose tungsten carbide bits with higher hardness and superior wear resistance; for soft rocks or fractured rock layers, carbide bits with moderate hardness and good toughness are suitable choices.
When using carbide rock drill bits, the following points should be noted:
Regularly check and replace severely worn drill bits to ensure rock drilling efficiency.
Reasonably control the impact force according to the rock properties and construction requirements to avoid excessive impact on the drill bit.
Ensuring the rock drill has good heat dissipation to avoid overheating the drill bit and affecting its performance.
Regularly maintain and repair the rock drill to extend its service life.
Conclusion
The application of cemented carbide in rock drill bits offers numerous advantages. It enhances rock drilling efficiency and construction safety while reducing construction costs and improving the environment. With the continuous advancement of materials science and technology, the performance of cemented carbide rock drill bits will continue to improve, offering robust support for the advancement of mining, tunneling, and building foundation construction.