Join us in advancing geotechnical engineering. Email: una@kellegco.com
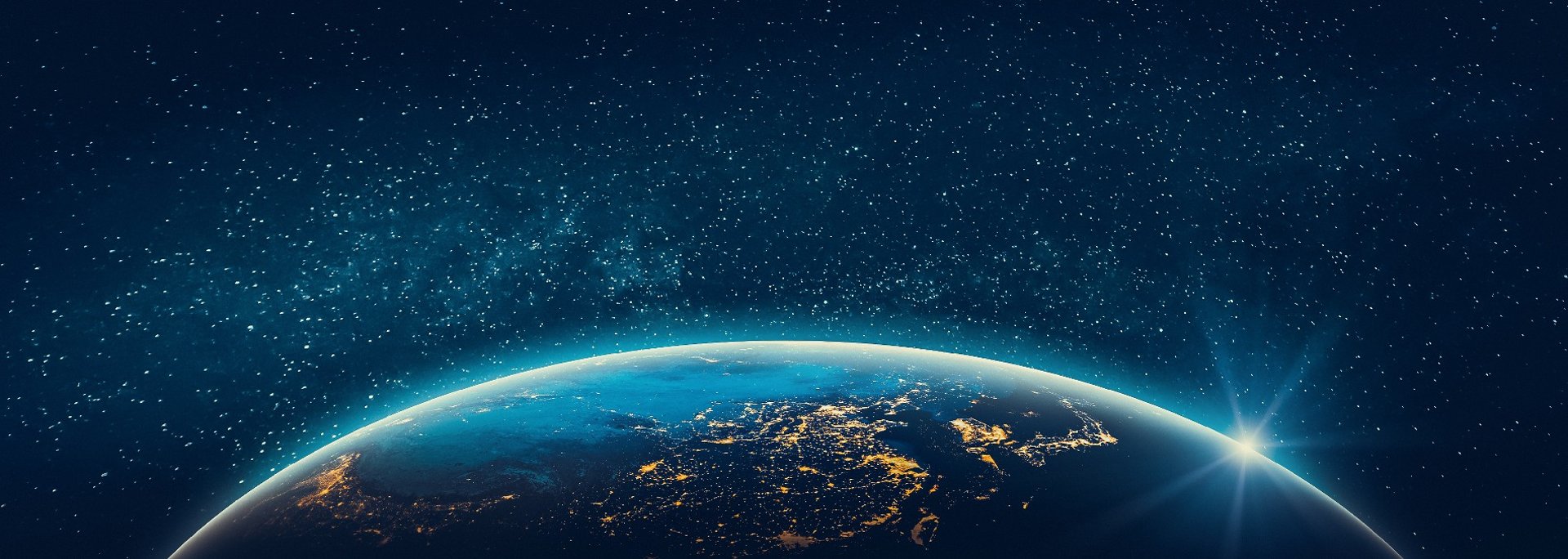
What Makes Tapered Bits Essential for Rock Drilling?
Tapered bits, including chisel bits and button bits, are widely used in a variety of challenging environments, from ore mining and tunnel engineering to roadway excavation and stone quarrying.
Una
6/25/2024
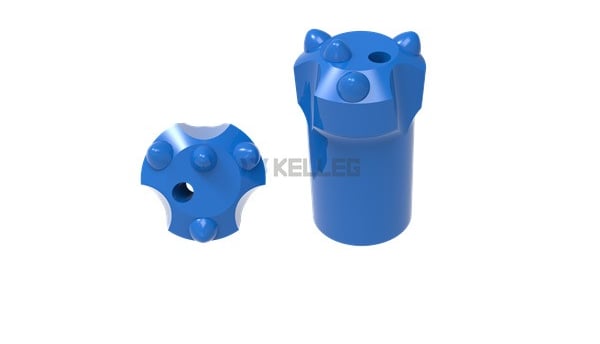
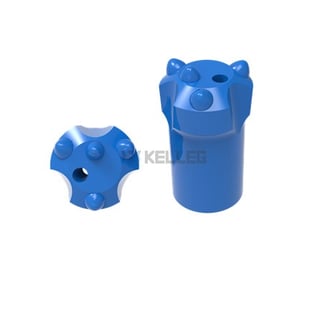
At the heart of this burgeoning industry are tapered bits, a specialized type of drilling tool that has become increasingly essential for professionals in the mining, construction, and infrastructure sectors. These tapered drilling tools, which include both tapered bits and drill rods that allows for the efficient transmission of impact and rotation, making them indispensable for rock drilling applications.
Tapered bits, including chisel bits and button bits, are widely used in a variety of challenging environments, from ore mining and tunnel engineering to roadway excavation and stone quarrying. Their reliable performance and ability to handle a diverse range of rock formations have made them a crucial tool for industry professionals, helping to enhance drilling efficiency and overall project productivity.
Understanding Tapered Bits for Rock Drilling
Tapered bits are a type of rock drilling tool that feature a unique design on the shank or body of the bit. This tapered configuration allows the bit to be securely connected to the drill rod, enabling the efficient transmission of impact and rotational forces from the drilling equipment to the rock face. The taper design provides a reliable and stable connection, ensuring that the drilling forces are effectively transferred to the rock, resulting in improved drilling efficiency and performance.
Advantages of Tapered Bits
Firstly, the secure connection between the bit and the drill rod ensures that the impact and rotational forces are accurately transmitted, minimizing energy losses and maximizing the drilling effectiveness. This translates to improved drilling efficiency and faster penetration rates. Additionally, the tapered configuration provides a stable and durable connection, making tapered bits less prone to becoming dislodged or damaged during the drilling process. This enhanced reliability and durability contribute to the overall longevity and performance of the rock drilling tools.
Principle of Operation for Tapered Rock Drilling Tools
The principle of operation for tapered rock drilling tools lies in their ability to effectively transmit the impact and rotational forces from the drilling equipment to the rock face. This precise transmission of forces is crucial for maximizing the drilling effectiveness and achieving optimal results. By accurately conveying the impact and rotation to the rock, tapered bits enhance the overall efficiency and performance of the rock drilling tools, enabling faster and more reliable penetration.
Impact and Rotation Transmission
This precise transmission of forces is crucial for maximizing the drilling effectiveness and achieving optimal results. By accurately conveying the impact and rotation to the rock, tapered bits enhance the overall efficiency and performance of the rock drilling tools, enabling faster and more reliable penetration.
Connection with Drill Rods
The taper on the bit's shank or body allows for a secure and stable interface with the corresponding taper on the drill rod. This interlocking connection ensures a reliable and durable coupling, preventing the bit from becoming dislodged or misaligned during the drilling process. The stable connection between the tapered bit and the drill rod contributes to the overall stability and reliability of the rock drilling tools, enabling consistent and efficient drilling operations.
Types of Tapered Bits
Chisel bits are commonly used in a wide range of applications, including mining, tunnel engineering, roadway excavation, and stone mining. Their tapered configuration and cutting edges are optimized for efficiently breaking and removing rock material, contributing to the overall efficiency and productivity of rock drilling operations.
Chisel Bits
Tapered chisel bits are well-suited for a variety of mining applications, from ore mining to mineral extraction. Their reliable connection and efficient drilling performance make them essential for maintaining high productivity and cost-effectiveness in these operations. Additionally, chisel bits are widely employed in tunnel engineering projects, where their ability to effectively drill through rock formations is crucial for the construction of critical infrastructure.
Button Bits
The button bit is characterized by its distinctive cutting elements, which are typically made up of a series of carbide buttons or inserts embedded in the bit's face. These button-style cutting elements provide enhanced durability and wear resistance, making them well-suited for applications in challenging rock formations or abrasive drilling environments. Tapered button bits are commonly used in mining, construction, and other rock drilling applications where high performance and extended tool life are essential.
Applications of Tapered Bits
Mining
Tapered bits are widely used in the mining industry, where they play a crucial role in the extraction of valuable resources from the earth. In both open-pit and underground mining operations, tapered drilling tools are employed to drill holes for the placement of explosives or to facilitate the removal of rock and ore. Tapered bits are essential for maintaining high productivity and cost-effectiveness in mining operations, as they contribute to the overall efficiency and performance of the rock drilling tools.
Tunnel Engineering
In the field of tunnel engineering, tapered bits are also widely used for rock drilling tasks. The construction of tunnels, whether for transportation, utilities, or other infrastructure projects, often requires the drilling of holes in rock formations. Tapered bits, with their secure connection to the drill rods and efficient force transmission, are well-suited for these applications. They enable the drilling crew to effectively break through the rock and create the necessary openings for the tunnel construction. The use of tapered bits in tunnel engineering helps to improve the overall efficiency, productivity, and safety of these critical infrastructure projects.
Roadway Excavation
Tapered bits also find application in the excavation and construction of roadways. The development of new roads, highways, and other transportation infrastructure often involves drilling into rock formations to create the necessary foundations and clearance. Tapered bits, with their reliable connection and efficient force transmission, are valuable tools in these roadway excavation projects. They allow construction crews to effectively drill through the rock, enabling the smooth progression of the road construction process. The use of tapered bits in roadway excavation contributes to the overall efficiency, productivity, and quality of the final infrastructure.
Stone Mining
The versatility of tapered bits extends to the field of stone mining, where they are utilized in quarry operations and the extraction of natural stone resources. This enables quarry workers to efficiently break through the rock and extract the desired stone materials. The use of tapered bits in stone mining helps to improve the overall productivity and cost-effectiveness of these operations, as they contribute to the efficient and reliable drilling of the rock formations.
Selecting the Right Tapered Bit
When selecting the appropriate tapered bit for rock drilling, the properties of the rock being drilled are a crucial consideration.
Factors such as the hardness, brittleness, and abrasiveness of the rock can significantly impact the performance and wear-resistance of the drilling bits. For instance, hard rock formations may require tapered bits with enhanced wear-resistance, while softer rock can be effectively drilled using bits that prioritize faster penetration rates. Understanding the specific rock properties of the drilling site allows professionals to choose the tapered bit that is best suited for the application, maximizing the efficiency and productivity of the rock drilling operations.
Drilling Method
The drilling method employed is another important factor in selecting the right tapered bit for rock drilling tools.
Different drilling techniques, such as rotary drilling and impact drilling, have varying requirements for the design and performance of the drilling bits. Rotary drilling, for instance, may benefit from tapered bits with excellent wear resistance and stability, while impact drilling may call for bits capable of withstanding high-impact loads. Carefully matching the tapered bit design to the specific drilling method being used is crucial for ensuring optimal drilling efficiency and minimizing the risk of premature bit failure.
Bit Size
The size of the tapered bit, including its diameter, length, and other key parameters, is another important factor to consider when selecting the right tool for rock drilling applications.
The bit size directly affects the drilling efficiency, hole size, and the overall compatibility with the drilling equipment. When choosing the appropriate tapered bit size, professionals must carefully evaluate the required hole diameter, desired drilling speed, and the capabilities of the drilling machinery. By selecting the optimal bit size for the specific application, users can maximize the productivity and effectiveness of their rock drilling tools.
Material and Design Considerations for Tapered Rock Drilling Tools
The material quality of tapered rock drilling tools is a critical factor that directly impacts their performance, durability, and service life. High-quality materials, such as advanced steel alloys and carbide composites, are essential for ensuring the wear and impact resistance of the tapered bits. These materials can significantly extend the lifespan of the tapered bits, allowing them to withstand the demanding conditions of rock drilling operations without premature failure. The use of superior materials in the manufacturing of tapered rock drilling tools contributes to their overall efficiency, reliability, and cost-effectiveness.
Structural Design
The structural design of tapered rock drilling tools is another key factor that influences their performance and effectiveness. The shape, arrangement, and placement of the cutting elements, such as carbide inserts or buttons, play a crucial role in the bit's rock-breaking efficiency. A well-designed tapered bit with an optimized structural configuration can improve the crushing and penetration capabilities of the drilling tool, reducing energy losses and enhancing overall drilling productivity. The careful consideration of the bit's structural design, in addition to the material quality, helps to ensure the delivery of superior performance and efficiency in rock drilling applications.
Conclusion
Tapered bits have firmly established themselves as an essential component of rock drilling tools, offering a range of benefits that make them indispensable across various industries and applications. Their secure connection with the drill rods, efficient transmission of impact and rotation, and suitability for diverse rock formations have solidified their role as a crucial tool for professionals in the mining, construction, and infrastructure sectors.
By understanding the principles of operation, types, and selection factors for tapered bits, we can optimize the performance and productivity of our rock drilling tools, ensuring the successful completion of challenging projects. The ongoing developments in material quality and structural design further reinforce the importance of tapered bits in the ever-evolving field of rock drilling technology.
As we continue to push the boundaries of rock drilling efficiency and performance, the role of tapered bits remains paramount. Their ability to deliver reliable and efficient drilling, coupled with their versatility across diverse applications, makes them an indispensable component in our quest for success in the mining, construction, and infrastructure industries.