Join us in advancing geotechnical engineering. Email: una@kellegco.com
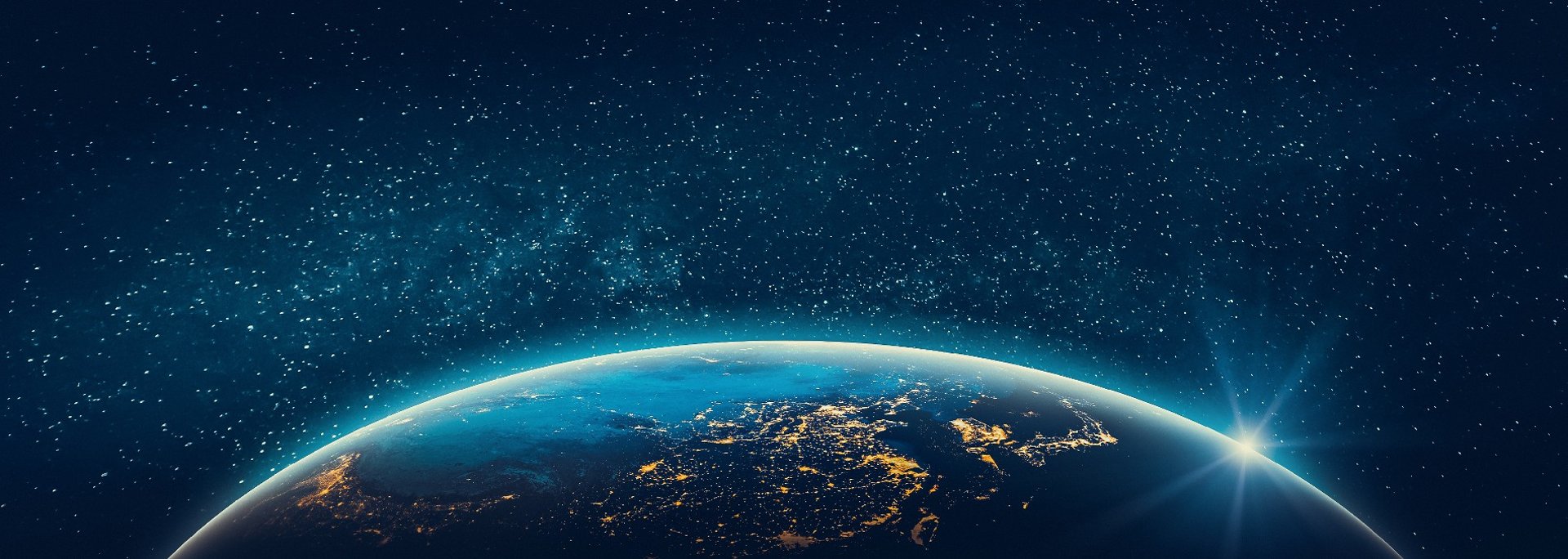
5 Key Benefits of Using Retrac Button Bits in Rock Drilling
Retrac button bits assist to overcome typical difficulties and enhance drilling performance by offering a consistent and effective answer for rock drilling.
Una
8/8/2024
Introduction
One of the special difficulties of rock drilling is handling different rock kinds ranging from loose and fragmented to hard and abrasive. While loose or fractured formations might allow parts to get caught or result in borehole instability, hard rocks can rapidly dull tools. These problems draw attention to the need of employing specialist, premium tools meant to manage severe drilling conditions.
Excellent answers to these problems are retrac button bits. Designed especially for rock drilling, these bits include a retrac skirt body that keeps the bit from being caught in loose or fractured rock—a typical issue causing major delays and expenses. Retrac button bits also provide durability and a longer lifespan as they are engineered to resist the demanding environments sometimes faced in rock drilling.
Any rock drilling project depends on the success of which depends on the choice of bit. The efficiency of the drilling process, the quality of the borehole, and the general operation's cost-effectiveness may all be much influenced by the suitable bit. Incorrect bit use could result in frequent bit changes, more equipment wear and tear, even project delays. Thus, choosing a bit that fits the particular rock type and circumstances you are working with is really vital.
Retrac button bits assist to overcome typical difficulties and enhance drilling performance by offering a consistent and effective answer for rock drilling. Choosing the correct bit will help you to guarantee effective, safe, and within budget completion of your drilling operations.
1. Enhanced Durability and Longevity
Built for longevity, retrac button bits are perfect for difficult rock drilling projects. Made from premium materials like tungsten carbide, which is renowned for its extraordinary hardness and resilience, these pieces This building guarantees the bits' ability to survive the abrasive conditions usually seen in rock drilling, therefore enabling them to meet the requirements of the work.
One of the main elements improving the lifetime of these parts is the retrac skirt body design. It lessens general tension during drilling and keeps the bit from being caught in loose or broken rock. By helping to reduce wear on the cutting edges and buttons, this design lets the bit remain effective for a longer time.
These pieces' deliberately placed and designed buttons help to spread the impact equally, therefore lowering the chance of early wear and damage. This careful engineering increases the bit's lifetime, therefore reducing the need for regular replacements and saving money. Any rock drilling project would benefit from Retrac button bits as they provide dependable, long-lasting performance in the most demanding drilling conditions.
2. Improved Drilling Efficiency
Especially when working on hard and abrasive rock formations, maximizing performance and lowering costs depend on improved drilling efficiency. Thanks to greatly enhanced modern drilling technologies, tools that shine in breaking through difficult materials are Because they are especially made to meet the difficulties presented by hard rock, advanced drill bits have more lifetime and efficiency. Better penetration rates and general longevity of these bits will let drilling activities go more easily and with more dependability.
One main benefit of these technical developments is the lower downtime connected with regular bit changes. Not only slowed down the process but also raised expenses as conventional drilling techniques sometimes needed frequent stops to replace worn-out bits. Bit frequency has dropped dramatically as more robust and effective drilling tools have evolved. Less interruptions and a more continuous drilling process resulting from this aid to preserve production and save running expenses.
Moreover, contemporary drilling equipment preserve a constant drilling speed and performance, which increases general output. These tools provide uniformity, therefore guaranteeing faster and more effective completion of tasks. Faster project completion and improved overall outcomes follow from drilling teams depending on this consistent performance to achieve project objectives and timelines.
These developments in drilling technology help to provide smoother, more efficient operations, therefore facilitating handling of difficult rock formations and resulting in less time required.
3. Superior Performance in Unstable Rock Conditions
Drilling in unstable rock conditions presents significant challenges, but recent advancements have greatly improved performance in these situations. Unstable rocks, such as loose or fragmented material, can make drilling more difficult and increase the risk of problems. Specialized drilling tools and techniques have been developed to tackle these issues more effectively.
One of the key innovations is the retrac button bit. This tool is designed to handle unstable rock by reducing the likelihood of the drill becoming stuck or buried. Its design allows for smoother penetration and better stability, even in challenging conditions. The button bits are particularly useful because they enhance the ability to drill through loose rock without frequent interruptions or equipment failures.
In addition to advanced tools, modern drilling techniques are crucial for dealing with unstable rock. Features like retractable skirt bodies help in retrieving drill tools more effectively if they become stuck. This feature not only aids in recovery but also helps maintain the straightness of the borehole, which is important for accurate drilling.
Working with unstable rock also calls for careful control of drilling settings. Changing factors including drilling speed, pressure, and fluid circulation lets operators fit the new circumstances. This adaptability makes sure the drilling operation stays successful and efficient even with challenging rock formations.
These developments in equipment and methods simplify and dependability drilling in unstable rock environments. They help to increase drilling efficiency and lower the likelihood of complications during operations by addressing the special difficulties presented by loose or fragmented material.
4. Versatility Across Different Rock Types
Retrac button bits are incredibly versatile and can handle a range of rock types, from hard and dense to fractured and unstable. This adaptability is crucial for drilling operations that encounter various geological conditions. Whether you’re working through solid rock or navigating broken materials, these bits maintain their performance, making drilling more efficient and reliable.
Their versatility extends across several industries. In mining, retrac button bits are used to extract minerals from different rock formations, allowing operations to run smoothly despite changes in rock type. In quarrying, these bits help break down rock for construction and landscaping, ensuring that projects can proceed without delays caused by changing rock conditions.
The ability of retrac button bits to handle diverse rock types means fewer interruptions and less need for different drilling equipment. This not only improves efficiency but also reduces downtime, making them a practical choice for various drilling tasks. Their consistent performance across different rock conditions highlights their importance in both mining and quarrying operations.
5. Enhanced Safety and Reliability
Especially under demanding situations, retrac button bits are very essential for increasing dependability and safety in drilling operations. These parts are made to run reliably even through hard or unstable rock. This consistent functioning helps prevent unanticipated issues that can cause equipment breakdown or mishaps.
Retrac button bits mostly benefit from their capacity to withstand demanding environments without sacrificing performance. Reducing the possibility of equipment failures and operational disturbances depends on this dependability. When drilling tools perform as predicted, there is less possibility of dangerous circumstances arising, thereby preserving a safer workplace.
Safe and flawless operations depend on reliable tools. Unreliable drilling tools can cause delays, raise downtime, and compromise safety. Retrac button bits operate well over several rock kinds and situations, therefore helping to avoid these problems. A safer and more effective workplace results from less equipment failures and less need for regular adjustments or replacements.
Retrac button bits also help drilling projects be successful generally by offering constant performance. They follow safety guidelines and assist to guarantee that projects go on without incident and on time. Their dependability helps to ensure the safety of the workplace as well as the drilling process's effectiveness, so they are quite vital components of effective drilling operations.
Conclusion
Retrac button bits have a number of advantages, making them a great choice for rock drilling. They increase efficiency by cutting through harder and abrasive rocks more effectively. This lowers the need for frequent bit replacements and allows drilling operations to continue uninterrupted.
These parts also work remarkably effectively in unstable rock environments. Their design helps to keep the drill from being trapped or buried in loose or cracked rock, which not only enhances drilling performance but also makes the workplace safer by lowering the chance of accidents caused by equipment failure.
Retrac button bits also provide great flexibility. From solid to fractured formations, they can manage a wide spectrum of rock types, which makes them important in mining, quarrying, and building among other sectors. Their adaptability to many rock conditions qualifies them for several drilling uses.
Their dependable performance under difficult conditions promotes both safety and efficiency. Retrac button bits contribute to the successful and timely completion of drilling operations by ensuring consistent performance even in tough circumstances.
Choosing the correct drilling equipment is critical for attaining optimal results. Retrac button bits are an excellent choice because to their versatility, performance, and safety features.
If you need reliable drilling tools, Retrac button bits are a great choice. Please contact us if you want further information or wish to make a purchase. Our staff is ready to assist you in selecting the right tools for your drilling requirements.
FAQs
1. What are the Retrac button bits?
Retrac button bits are drill bits that are specifically intended for harsh rock environments. They are designed to handle a variety of rocks, including hard, abrasive, and unstable formations.
2. How can Retrac button bits increase drilling efficiency?
They increase efficiency by cutting through hard and abrasive rocks more efficiently, reducing the need for frequent bit replacements and ensuring that operations operate smoothly.
3. Can Retrac button bits be utilized in unstable rock environments?
Yes, they are particularly engineered to manage unstable rock situations such as loose or cracked rock, minimizing the likelihood of the drill becoming stuck and enhancing overall performance.
4. Which industries often employ Retrac button bits?
These bits are widely utilized in mining, quarrying, and building, when drilling through difficult rock formations is required.
5. How can Retrac button bits improve safety?
Their continuous performance in tough conditions contributes to fewer accidents and equipment breakdowns, making the workplace safer.
6. What makes the Retrac button bits versatile?
They can handle a wide range of rock types, from solid to fractured, making them suited for a variety of drilling applications.
7. How do Retrac button bits handle rough and abrasive rocks?
They are made of strong materials and have innovative features that allow them to cut through difficult and abrasive rocks with ease.
8. What should I consider when selecting a Retrac button bit?
When selecting a Retrac button bit, evaluate the kind of rock, necessary depth, and jobsite circumstances to determine the appropriate bit.
9. How do I buy Retrac button bits?
Contact us for additional information or to make a purchase. We're here to assist you select the best bit for your requirements.
10. Who can I contact for help or additional information about Retrac button bits?
Contact our customer service staff for assistance or further information. We are here to answer your questions and give the support you require.
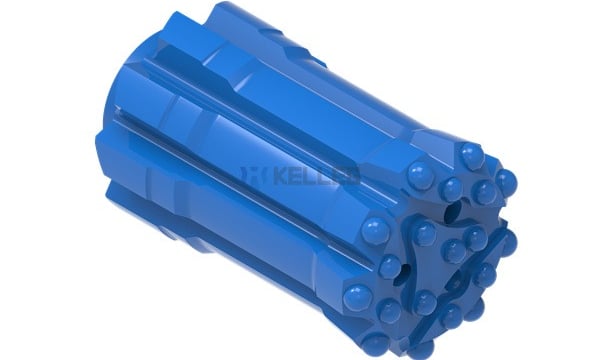
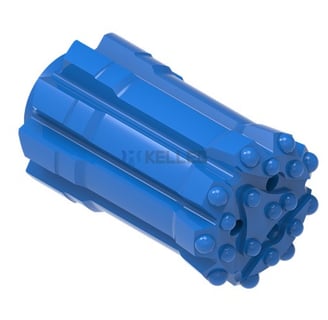